Leveraging automated solutions for increased ecommerce demand
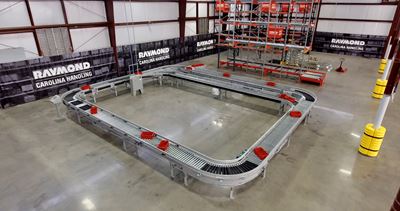
The impacts of COVID-19 and soaring e-commerce demands have massively accelerated plans for both distribution centers and manufacturers, and have pushed robotics technologies such as automated guided vehicles (AGVs) and autonomous mobile robots (AMRs) to the forefront.
By Chris Youngs, Corporate Manager, Intralogistics Solutions Group, Carolina Handling, a Raymond Solutions and Support Center
The impacts of COVID-19 and soaring e-commerce demands have massively accelerated plans for both distribution centers and manufacturers, and have pushed robotics technologies such as automated guided vehicles (AGVs) and autonomous mobile robots (AMRs) to the forefront. Many operators who thought they had plenty of bandwidth for growth, throughput, and capacity are trying to quickly reconfigure to meet demand.
Consequently, the material handling industry has seen more growth in automation and robotics in North America in the last five to seven years than in the previous 30 years combined. More and more people are turning to e-commerce to procure products, skyrocketing the sheer volume of goods that are moving throughout the supply chain.
The rapid proliferation of e-commerce has rapidly changed consumer expectations as well. A few years ago, a three-day span from order to delivery was the norm. However, as the use of e-commerce has become ubiquitous, customers are now looking for two-day, one-day and, in some categories, same-day delivery.
What does this mean for material handling operations? With some e-commerce customers reporting year-over-year growth rates of 20%, 30% and even 40% in recent years, many logistics and supply chain managers have seen their three-to-five-year plans rapidly pulled ahead.
Facing increased competitive demands and consumer expectations amid labor shortages, rising labor costs and high turnover, many companies are shifting from person-to-goods processes (where people retrieve goods) to automated, software-driven, goods-to-person processes and technologies. Additionally, many manufacturers traditionally working in a business-to-business model are now facing pressure to ship directly to consumers.
To meet those expectations, midsize and small companies must now respond to compete and survive. Many are changing their internal processes to an automated system that retrieves goods from racks or implementing a shuttle-based, AMR or AGV system. The tipping point in favor of automation has arrived for companies with two or three shifts, or with thousands or tens of thousands of items moving each day.
One of the biggest challenges for both B2B and B2C companies is the exponential increase in SKUs. Driven by consumer demand for greater variety, mergers and acquisitions, new product lines and smaller batch producers, the resulting increase has stretched facilities and added complexities. This also has led to an increase in advanced picking technologies, including operator assist, robotics, automated storage and retrieval systems and AGVs.
But how do companies successfully implement automation? Essential elements in developing an appropriate plan for automation are understanding what customers currently do, the processes in use and the anticipated outcome.
Some customers look to reduce labor costs, while others focus on ergonomics and safety. Using automation for simple repetitive tasks can permit allocation of people to more useful reasoning functions. One advantage for small and midsize companies is their ability to develop and implement innovative systems in a nimbler fashion than the larger hubs.
When looking to implement automation in your facility, it’s important to work with a trusted partner who will take the time to understand your unique application needs before recommending solutions. This will help ensure the solutions are a good fit for your facility and a good investment for your business.
Chris Youngs is Corporate Manager, Intralogistics Solutions Group at Carolina Handling, a Raymond Solutions and Support Center.
Carolina Handling was pleased to contribute to the Plant Services blog in March. To read this and other blogs please visit, the Plant Services blog page.