South Carolina Conveyor Systems Supplier
AS/RS systems and conveyors can elevate the efficiency of your warehouse, enhance safety practices and substantially reduce employee costs.
Today’s conveyor systems can move everything from lightweight cartons to heavy pallets within your facility, and they are an integral part of modern material handling design.
Conveyors fall into three separate categories for the vast majority of material handling systems:
- Powered roller or belt systems (for carton handling)
- Powered chain or roller conveyors (for pallet handling)
- Non-powered conveyor systems
Powered Package Handling Roller or Belt Conveyors
Powered belt or roller conveyor systems are frequently used for smaller items like cartons and packages.
Belts are mostly used for advancing products along a line, while rollers are used for accumulating packages in certain areas along the line.
Belt Conveyors
In use since the early 1900s, conveyor belts are a fundamental part of most material handling systems. Not as costly as roller systems and oftentimes more appropriate for specific functions like advancing lightweight products, conveyor belts are used in many material handling configurations.
Belt conveyors feature a long, looped belt that is positioned on the top of a series of non-powered rollers on a metal substructure called a slider belt. A motor drives a pulley that turns the belt and advances items down the conveyor line.
Belts can be made of a variety of surfaces and materials in accordance with the function and role of the conveyor. For instance, a conveyor belt surface might be totally flat in segments where items need to glide off the line and may have a ridged texture on segments where items have to be transported up inclines.
Roller Conveyors
While belt conveyors still have a place in most operations, newer roller conveyors offer a host of more useful benefits in many modern material handling uses.
First and foremost, roller configurations can enable collection of objects on the line where belt conveyors cannot. This is a meaningful distinction because there are countless scenarios where objects must slow down and accumulate in material handling applications. Accumulation is often necessary when objects must be paused before being relayed to automated palletizers or sorters.
Advanced roller conveyors also have the capacity to supervise products on the line and implement zero pressure accumulation, meaning none of the products collecting on the line touch each other as they decelerate and finally stop.
Roller systems are made up of numerous cylindrical rollers that are generally set up in one of three different ways:
- Line shaft conveyors: In a line shaft conveyor, a long steel shaft runs beneath the cylinders perpendicular to them and is joined to each roller with rubber O-rings. A drive mechanism rotates the shaft and, accordingly, drives the cylinders by way of the connected O-rings. Line shaft conveyors are the most inexpensive of all roller conveyors, but they also require the most maintenance because the connections between the shaft and rollers need frequent readjustment and sometimes fail.
- Belt-driven roller conveyors: As you would surmise from the name, belt-driven roller systems are powered by a belt mechanism that sits beneath the roller platform. A motor drives the belt, which advances the cylinders.
- MDR conveyors: Motorized roller conveyors, sometimes referred to as motor-driven roller (MDR) conveyors, are set up in sections where a single cylinder from each segment is powered by its own power source. That solitary motor-driven roller is connected to the others in that segment via flexible O-rings, thereby powers all the rollers in the section. Motorized sections are placed in succession to configure the conveyor line.
MDR systems are known for their energy efficiency because: a.) They usually are powered by 24-volt direct current motors and b.) The motors can be set up to engage only when an object is detected on the cylinders, meaning they are motionless throughout much of the day.
Although MDR conveyors are more expensive than belt drive and line shaft systems, energy expenses and maintenance expenses are typically quite a bit lower than the other options mentioned. - Segmented belt conveyor: The concept of motor-driven roller systems eventually led to the development of segmented belt conveyors. Similar to MDR systems, segmented belts operate independently and offer a lot of the same advantages of motor-driven rollers, including accumulation potential.
Powered Pallet Handling Conveyors
Powered pallet handling conveyors are frequently paired with automatic palletizers and AS/RS setups. Pallet handling conveyors can usually accommodate pallets of up to 4,000 pounds and proceed at a much slower pace than package handling systems, sometimes at speeds as low as four pallets per minute.
Pallet handling conveyors come in a couple of varieties: roller conveyors and chain conveyors.
- Pallet handling chain conveyor: Perhaps the most rudimentary of all conveyor systems, pallets on a chain conveyor line are placed on top of segments of heavy-duty chain. Motors propel the chain segments which in turn advance the pallets along the line.
- Pallet handling roller conveyor: Comparable to MDR conveyors, pallet handling roller configurations use larger rollers and heavy-duty chains to join the powered cylinder to the rest of the rollers in a conveyor unit.
Non-Powered Conveyors
Roller or skatewheel conveyors are the most common types of non-powered conveyors used in material handling. Non-powered rollers or skatewheels use inertia and gravity to move smaller loads through warehouses, pick modules, workstations, automated sorters, package-sorting areas and loading docks.
Skatewheel conveyors are made up of many independent wheels and need minimal energy to maintain the inertia of items as they progress along a conveyor line. On the whole, they move products quicker than non-powered roller configurations, and they have more versatility when it comes to setup. Given that they’re standalone wheels instead of a belt, they may be applied in curvilinear sections of a conveyor arrangement.
In general, non-powered roller conveyors are less expensive than skatewheel conveyor configurations. They are often utilized for workstations, pick modules and other sectors where it’s useful to have a flat surface to work on. Roller systems also slow products down that are coming from higher speed systems like sorters so that human laborers can keep up with conveyor performance.
Non-powered conveyors have a serious disadvantage in comparison to powered systems: By employing gravity and inertia to move materials, you lose the ability to directly manage the force applied to those items. In other words, you don’t have control of the speed and inertia of products on your line.
Conveyor Companies Near Me
If you’d like a complete evaluation of conveyor system possibilities for your warehouse, DC or other material handling operation, speak with an expert at Carolina Handling.
-
-
Proudly serving
Greenville, Simpsonville,
Easley, Greer, Spartanburg,
Gaffney, Clemson, Anderson,
Greenwood, Rock Hill, Lancaster,
Fort Mill, Newberry,
Piedmont, Mauldin,
and the entire State of South Carolina.
You May Also Like:
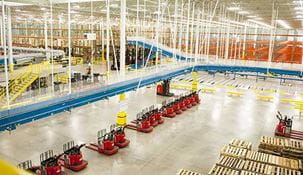
Automation
Carolina Handling can help you automate every aspect of your warehouse operation to increase efficiency.
Learn More
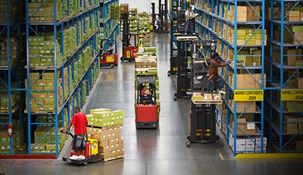
Optimization
Optimize everything in your warehouse to improve productivity and reduce operating costs.
Learn More
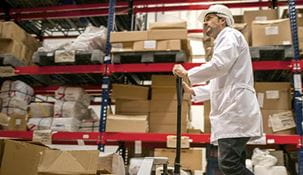
Warehouse Products
Looking for the right product for your operation? We have everything you need to do business in stock.
Learn More
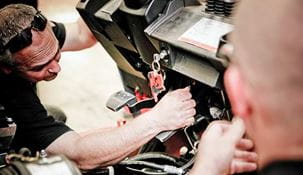
Service Maintenance
Providing superior lift truck service and maintenance for our customers is Carolina Handling's highest priority.
Learn More